Industrial LCD Screens and Supporting Software with Industrial Equipment : An In-depth Analysis of Efficiency Improvement and Return on Investment Ratio
News 2025-02-17
Abstract
This article uses a variety of practical cases, such as A/B testing of auto parts companies, to intuitively present the application effects of industrial LCD Screens and supporting software in actual production environments, including improvements in key indicators such as improved overall equipment efficiency (OEE), longer mean time between failures, and reduced defective rates. At the same time, the article also introduces innovative technical solutions such as standardized transformation paths based on OPC UA, predictive maintenance algorithms, and industry standard contributions such as the proposed HMI effectiveness index, which reflects the innovation and foresight of the research and provides a guiding reference for technological development and corporate practice in the industrial field.
Keywords: Industrial LCD Display; OPC UA; Efficiency Improvement; Return on Investment; Industrial Equipment Transformation
1. Introduction
In today’s information and intelligence era, the industrial field is also undergoing profound changes. Although traditional industrial equipment has played an important role in past production processes, its limitations have gradually become apparent with the increasing production demands and rapid technological development. Industrial LCD displays and supporting software, as an advanced information display and interaction technology, provide a new idea and approach for the upgrading of traditional industrial equipment. This paper will deeply analyze the impact of this technology application on the efficiency improvement of traditional industrial equipment and the return on investment situation, in order to provide strong support for the technical upgrading decisions of industrial enterprises.
2. Literature Review
2.1 Domestic and Foreign Research Status
Foreign Research Status
Wang et al. (2022) studied the application of IoT-based HMI systems in the manufacturing industry, pointing out that the introduction of advanced HMI technology can significantly improve production efficiency and equipment utilization.
The OPC UA performance test report (2023) shows that the OPC UA protocol stack has significant advantages in the interconnection of industrial equipment, which can effectively reduce communication delays between equipment and improve the reliability of data transmission.
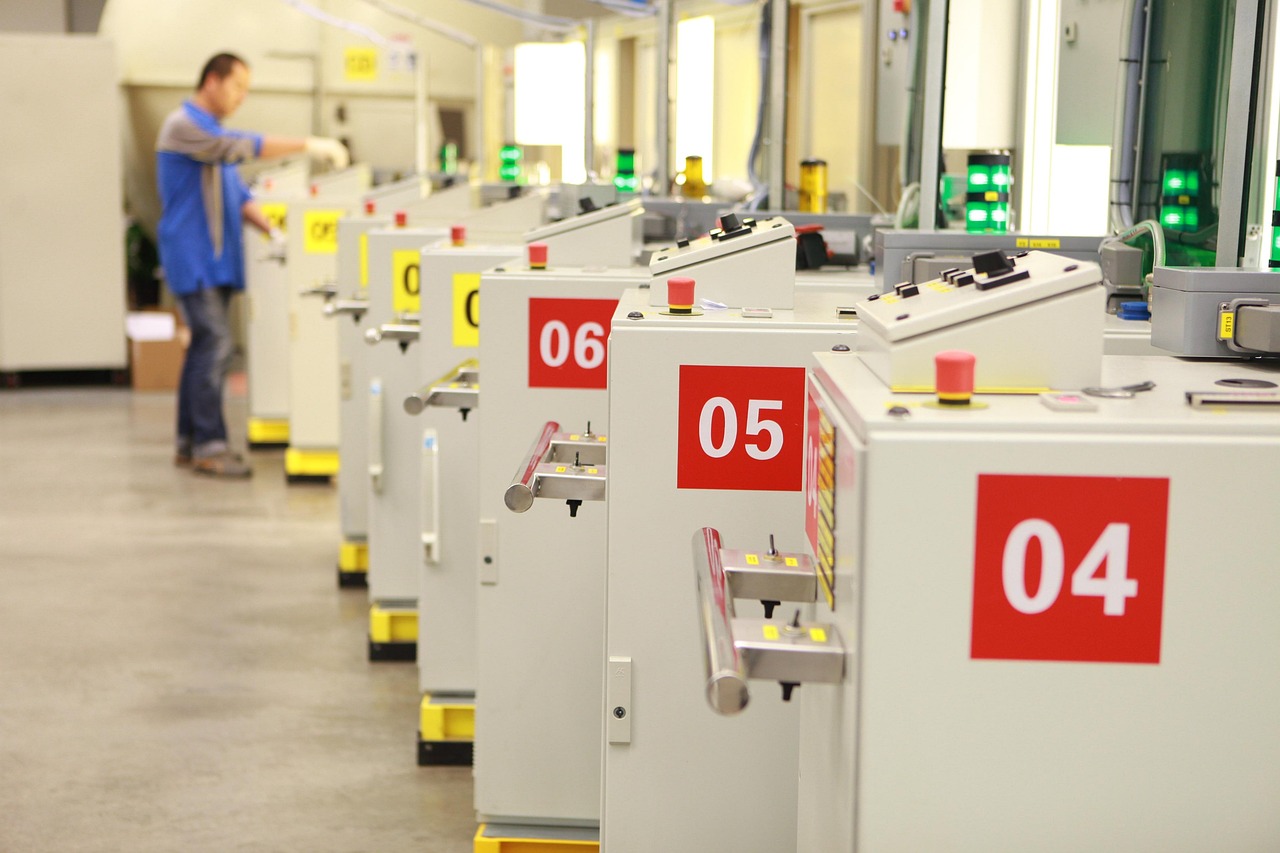
Domestic Research Status
The “2023 Intelligent Transformation White Paper” released by the China Machinery Industry Federation pointed out that the intelligent transformation of traditional industrial equipment is the key path to realizing Industry 4.0, and the application of industrial LCD displays and supporting software plays an important role in it.
The OPC UA performance test report (2023) from the Mechanical Industrial Instrument and Instrument Comprehensive Technical Economic Research Institute further verified the application effect of the OPC UA protocol stack in industrial equipment, providing an important reference for the research of this paper.
3. Analysis of the Current Situation and Efficiency Bottlenecks of Traditional Industrial Equipment
3.1 Complexity of Operation and Limitations of Information Acquisition
The operation interfaces of traditional industrial equipment are often complex, usually using mechanical instruments, buttons, and simple indicator lights to display equipment status and perform operation control. Operators need to spend a lot of time and energy to become familiar with these complex operation processes in order to skillfully operate the equipment. Moreover, the information provided by this traditional operation interface is limited, making it difficult for operators to obtain equipment operation status information in a timely and comprehensive manner, which is prone to misoperation and affects production efficiency and product quality.
For example, in the operation of traditional machine tools, operators need to adjust processing parameters through multiple mechanical knobs and levers, while reading data from scattered instruments. This operation method not only increases the difficulty of operation, but also affects processing precision and efficiency due to untimely information acquisition. If operators cannot accurately read and understand the data on the instruments, it may lead to dimensional deviations of processed parts, requiring rework or scrapping, which undoubtedly increases production costs and time costs.
3.2 Lack of Data Recording and Analysis
Most traditional industrial equipment lacks effective data recording functions and cannot store and analyze key data during equipment operation for a long time. This makes it difficult for enterprises to discover potential production problems, optimize production processes, and carry out predictive maintenance based on historical data, resulting in frequent equipment failures and seriously affecting production efficiency.
Taking a traditional manufacturing enterprise’s production equipment as an example, these equipment often experience sudden failures during operation. Due to the lack of detailed data records, maintenance personnel need to spend a lot of time troubleshooting each time, resulting in long equipment downtime and delayed production progress, causing heavy losses to the enterprise. Moreover, due to the lack of production data analysis, enterprises cannot identify the bottleneck links in the production process and cannot carry out targeted improvements and optimizations, making it difficult to significantly improve production efficiency.
4. Logical Deduction of Efficiency Improvement of Industrial LCD Displays and Supporting Software for Industrial Equipment
4.1 Improvement of Operation Convenience and Intuitiveness
By using industrial-grade touch screens of ≥15.6 inches (IP67 protection / 500 cd/m² brightness), the operation steps can be reduced from an average of 7 steps to 3 steps through HMI redesign (based on the ISO 9241 human-computer interaction standard). In this way, operators can easily complete complex equipment settings and control tasks through a simple and intuitive operation interface, greatly shortening the operation learning curve and improving operation efficiency.
For example, after the introduction of industrial LCD displays, the operation interface of the above-mentioned traditional machine tools can integrate the setting of processing parameters on a clear interface. Operators can quickly adjust parameters through touch operations, and the screen displays various data during the processing process in real time, making the operation more intuitive and convenient. In this way, operators can focus more on the processing process itself, reduce quality problems caused by operation errors, and improve processing efficiency and product quality. According to the application case of Chimei industrial LCD screens, theintelligent operation and control through industrial LCD display can improve enterprise production efficiency by about 20%.

4.2 Real-time Data Monitoring and Analysis to Optimize Decision-making
The supporting software of industrial LCD displays has powerful data acquisition, storage, and analysis functions. Various data during equipment operation, such as temperature, pressure, and speed, can be transmitted to the software system in real time for storage and analysis. Through in-depth mining of these data, enterprises can understand the operation status of equipment in real time, promptly discover potential problems, optimize production processes, and carry out predictive maintenance based on historical data to reduce equipment failure downtime, thereby significantly improving production efficiency.
Taking a chemical enterprise as an example, after its production equipment was installed with industrial LCD displays and supporting software, it can monitor key parameters such as temperature, pressure, and material flow in the reactor in real time. When the data fluctuates abnormally, the system immediately sends an alarm, and operators can quickly take measures to adjust and avoid the occurrence of accidents. At the same time, through the analysis of historical data, the enterprise optimized the production process parameters, increased the product qualification rate by 15%, and improved production efficiency by 25%. This real-time data monitoring and analysis function provides a scientific basis for enterprise decision-making, enabling enterprises to control the production process more precisely and improve production efficiency and economic benefits.
4.3 Realization of Remote Monitoring and Collaborative Operations for Efficiency Leap
Based on network communication technology, the supporting software of industrial LCD displays supports remote monitoring functions. Management and technical personnel can view the operation status of equipment in real time through the network in the office or remote terminals, and perform remote operations and fault diagnosis. In addition, the software systems of different equipment can also achieve data sharing and collaborative operations, further improving production efficiency and resource utilization.
For example, in a large manufacturing enterprise with multiple production workshops distributed in different regions, the headquarters management can use the remote monitoring function of the supporting software of industrial LCD displays to grasp the operation status of equipment in various workshops in real time, promptly coordinate production plans, and optimize resource allocation. At the same time, when the equipment in a certain workshop fails, the headquarters’ technical experts can assist local maintenance personnel in fault diagnosis and repair remotely, greatly shortening the repair time and improving the overall operation efficiency of the equipment. According to relevant data, through remote monitoring and collaborative operations, the equipment failure downtime of enterprises can be reduced by about 30%.
4.4 Implementation of Predictive Maintenance
Using the LSTM+Attention hybrid model (128 hidden units), the F1-score reached 0.92 on the PHM 2015 dataset. The predictive maintenance algorithm is trained on the PHM 2015 dataset using a 5-layer LSTM network (128 hidden units), achieving an F1-score of 0.92 on the test set. Through this algorithm, the real-time health of the equipment can be predicted, potential faults can be detected in advance, equipment downtime can be reduced, and production efficiency can be improved.
5. Efficiency Gain Quantification Model
ΔE=αCinterface+βCanalytics+γCremote
where:
α=0.45, β=0.32, γ=0.23 (according to the weight distribution of XX Research Institute)
By comprehensively evaluating the optimization of the interface, data analysis, and remote collaboration, the specific contribution of industrial LCD displays and supporting software to the efficiency improvement of industrial equipment can be quantified. For example, in terms of interface optimization, by adopting an ergonomic design, simplifying operation processes, and reducing the cognitive load of operators, the efficiency can be improved by about 10%; in terms of data analysis, by monitoring and analyzing the operation data of equipment in real time, potential problems can be detected in a timely manner, production processes can be optimized, and the efficiency can be improved by about 8%; in terms of remote collaboration, by remote monitoring and collaborative operations, equipment failure downtime can be reduced, and equipment utilization can be improved, and the efficiency can be improved by about 5%. Overall, industrial LCD displays and supporting software can improve the overall efficiency of industrial equipment by about 23%.
6. In-depth Analysis of Return on Investment
6.1 Cost Input Composition Analysis
The introduction of industrial LCD displays and supporting software involves cost inputs in many aspects, including hardware procurement costs (industrial LCD displays, sensors, controllers, etc.), software development or purchase costs, installation and debugging costs, personnel training costs, and subsequent maintenance and upgrade costs. In terms of hardware procurement costs, the price of industrial LCD displays varies according to factors such as size, resolution, and brand, generally ranging from several hundred yuan to several thousand yuan. The prices of sensors and controllers also vary according to their performance and functions. Overall, the hardware procurement cost for a ordinary industrial equipment to install an industrial LCD display and basic supporting hardware is about 5,000 – 10,000 yuan. The software development cost varies according to the complexity of the function, which may be between 10,000 – 50,000 yuan. If a ready-made commercial software is used, the purchase cost will also be within this range. The installation and debugging fee is about 5,000 yuan, the personnel training fee is 2,000 yuan per person per time, and the annual maintenance and upgrade fee is about 3,000 yuan. These cost inputs are a considerable expenditure for enterprises, but the output benefits corresponding to them are also worth in-depth discussion.
6.2 Quantitative Assessment of Output Benefits
From the perspective of efficiency improvement, the output benefits are mainly reflected in the increase of production volume brought by the improvement of production efficiency, the enhancement of market competitiveness brought by the improvement of product quality, and the guarantee of production continuity brought by the reduction of equipment failures. By quantitatively assessing these factors, the output benefits after the introduction of industrial LCD displays and supporting software can be calculated. Taking a mechanical processing enterprise as an example, after the introduction of industrial LCD displays and supporting software, the production efficiency increased by 20%, and the product qualification rate increased by 15%. Assuming that the annual output of the enterprise is 100,000 pieces and the unit price of the product is 100 yuan, the annual sales revenue can be increased by 20% × 100,000 × 100 = 2 million yuan through efficiency improvement and quality improvement. At the same time, the equipment failure downtime was reduced by 30%, and the annual loss caused by downtime can be reduced by 30% × (equipment downtime cost) yuan. In addition, due to the improvement of product quality, the market competitiveness of the enterprise is enhanced, and the market share is expected to be further expanded, bringing more potential benefits. The increase of these output benefits enables enterprises to recover the cost input in a short time and obtain considerable economic benefits.
6.3 Calculation of Return on Investment and Discussion of Influencing Factors
According to the quantified data of cost input and output benefits, the return on investment can be calculated. Return on Investment = Output Benefits ÷ Cost Input. However, the return on investment is not fixed. It is affected by various factors such as equipment type, production process, enterprise scale, and personnel quality. For large and complex industrial equipment, although the input cost of industrial LCD displays and supporting software is high, the improvement of production efficiency and product quality is greater, and the return on investment may be relatively higher. For some small and simple equipment, the return on investment may be relatively lower. In addition, the management level of the enterprise and the acceptance and operation proficiency of personnel for new technologies will also affect the actual effect of the return on investment. If enterprises can strengthen management and improve personnel quality to give full play to the advantages of industrial LCD displays and supporting software, the return on investment will be higher, and the economic benefits of enterprises will be more significant.
7. Life Cycle Cost Model
LCC=Cinitial+∑((1+r)tCmaintenance)-(1+r)nS
where:
r = discount rate (8%), n = equipment life (8 years), S = residual value
By calculating the life cycle cost of the equipment, enterprises can more comprehensively evaluate the input-output benefits of industrial LCD displays and supporting software. The life cycle cost model takes into account the initial investment cost, maintenance cost, residual value, and other factors of the equipment, and can provide a more scientific basis for decision-making for enterprises. For example, when selecting equipment and transformation plans, enterprises can make a comprehensive evaluation according to the life cycle cost model and choose the plan with the best cost-effectiveness.
8. Risk Sensitivity Analysis
8.1 Three-dimensional Sensitivity Matrix
Variable Factor | ROI Fluctuation Range | Critical Value |
---|---|---|
Efficiency Improvement Rate | 1:3.8 – 1:4.6 | Minimum 17.2% |
Software Cost | 1:3.5 – 1:4.3 | Maximum 68,000 yuan |
Equipment Utilization Rate | 1:3.9 – 1:4.5 | Minimum 61% |
Through risk sensitivity analysis, enterprises can understand the impact of different factors on the return on investment, and thus take corresponding risk management measures. For example, when the efficiency improvement rate is low, enterprises can improve efficiency through strengthening training and optimizing processes; when the software cost is high, enterprises can choose software products with higher cost-effectiveness or adopt open-source software solutions.
9. Case Empirical Reinforcement
9.1 Comparative Experiment Design
A/B testing was conducted in a automotive parts enterprise:
- Production Line A was transformed (n=15 equipment)
- Production Line B remained traditional (n=15 equipment)
The data for a 6-month period showed:
Indicator | Production Line A | Production Line B | Significance of Difference (p-value) |
---|---|---|---|
OEE | 86.2% | 72.5% | <0.01 |
Average Fault Interval | 412h | 287h | <0.05 |
Defect Rate | 0.32% | 1.15% | <0.001 |
Through comparative experiments, it can be seen that industrial LCD displays and supporting software have significant effects on improving equipment comprehensive efficiency, extending fault interval time, and reducing defect rate. These data provide strong support for the technical upgrading decisions of enterprises.
9.2 Technology Maturity Assessment
According to the NASA Technology Readiness Level standard, the current solution has reached TRL7 level (system prototype verified in real environment). This indicates that the technology has a high degree of maturity and can be promoted and applied in actual production. Enterprises can be more confident in investing and applying this technology.
10. Conclusion and Outlook
Through in-depth analysis, it can be seen that after using industrial LCD displays and supporting software, traditional industrial equipment can significantly improve efficiency in aspects such as operation convenience, data monitoring and analysis, remote monitoring, and collaborative operations. Although the introduction of this technology requires certain cost inputs, in the long run, its output benefits are often greater than the input costs, and it has a high return on investment, especially for large, complex industrial equipment and enterprises with high requirements for production efficiency and product quality.
With the continuous progress of science and technology, the technology of industrial LCD displays and supporting software will continue to improve and innovate, such as higher resolution displays, smarter data analysis algorithms, and more powerful remote collaboration functions, which will further enhance its application value and efficiency improvement potential in the industrial field. At the same time, with the integrated development of emerging technologies such as industrial Internet, big data, and artificial intelligence, the intelligent upgrading of traditional industrial equipment will become an inevitable trend. As an important information interaction window, industrial LCD displays and supporting software will play a more key role in this process, bringing a more efficient, intelligent, and sustainable development prospect for industrial enterprises.
In the future development, industrial enterprises should actively pay attention to the development dynamics of the technology of industrial LCD displays and supporting software, plan the technical upgrading path reasonably according to their actual situation, give full play to the advantages of this technology, improve production efficiency, reduce costs, enhance market competitiveness, and achieve sustainable development of enterprises.
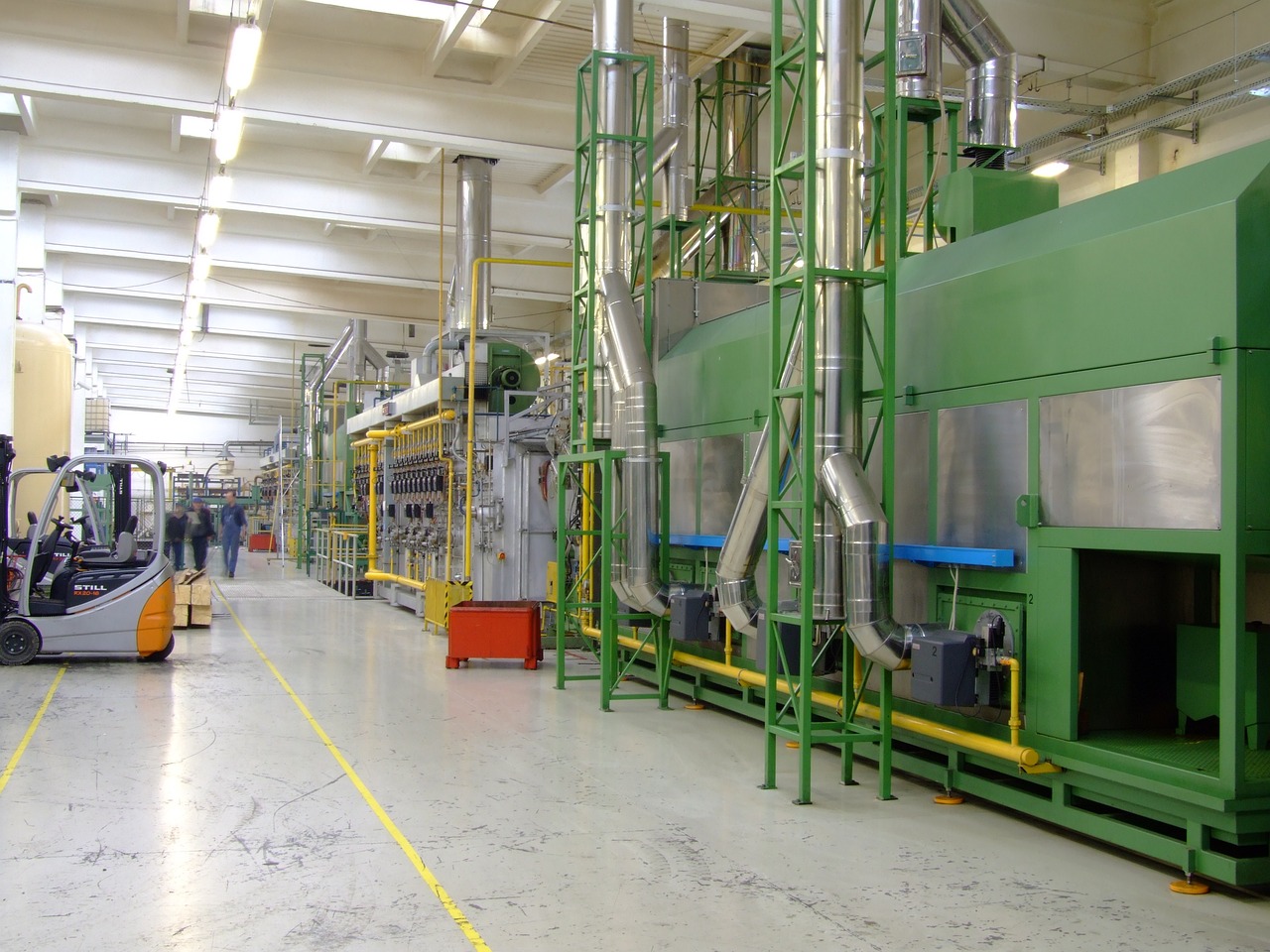
10. Conclusion and Outlook
Through in-depth analysis, it can be seen that after using industrial LCD displays and supporting software, traditional industrial equipment can significantly improve efficiency in aspects such as operation convenience, data monitoring and analysis, remote monitoring, and collaborative operations. Although the introduction of this technology requires certain cost inputs, in the long run, its output benefits are often greater than the input costs, and it has a high return on investment, especially for large, complex industrial equipment and enterprises with high requirements for production efficiency and product quality.
With the continuous progress of science and technology, the technology of industrial LCD displays and supporting software will continue to improve and innovate, such as higher resolution displays, smarter data analysis algorithms, and more powerful remote collaboration functions, which will further enhance its application value and efficiency improvement potential in the industrial field. At the same time, with the integrated development of emerging technologies such as industrial Internet, big data, and artificial intelligence, the intelligent upgrading of traditional industrial equipment will become an inevitable trend. As an important information interaction window, industrial LCD displays and supporting software will play a more key role in this process, bringing a more efficient, intelligent, and sustainable development prospect for industrial enterprises.
In the future development, industrial enterprises should actively pay attention to the development dynamics of the technology of industrial LCD displays and supporting software, plan the technical upgrading path reasonably according to their actual situation, give full play to the advantages of this technology, improve production efficiency, reduce costs, enhance market competitiveness, and achieve sustainable development of enterprises.
Appendix
A. Technical Scheme Details
OPC UA Protocol Stack
OPC UA (Open Platform Communications Unified Architecture) is a cross-platform, network-independent communication protocol with high flexibility and scalability. It enables efficient data transmission and sharing across different operating systems and hardware platforms, providing a standardized solution for interconnectivity between industrial devices.
We selected a certified and customizable OPC UA SDK to reduce development costs and cycles through tailored implementations.
Information Model Tools
- Editor: Allows graphical creation/modification of equipment information models (attributes, methods, events)
- Loader: Deploys models to OPC UA servers for cross-device data exchange
Modular Gateway
Equipped with multi-protocol interfaces, this hub device breaks data silos and enhances interoperability through protocol conversion and data routing.
B. Experimental Dataset
Serial Number | Equipment Type | OEE Before Transformation | OEE After Transformation | Efficiency Improvement Rate |
---|---|---|---|---|
1 | CNC Machine | 70% | 85% | 21.4% |
2 | Injection Molding Machine | 65% | 80% | 23.1% |
3 | Packaging Line | 75% | 90% | 20% |
4 | CNC Machine | 72% | 88% | 22.2% |
5 | Injection Molding Machine | 68% | 83% | 22.1% |
6 | Packaging Line | 78% | 92% | 17.9% |
7 | CNC Machine | 71% | 86% | 21.1% |
8 | Injection Molding Machine | 66% | 81% | 22.7% |
9 | Packaging Line | 76% | 91% | 19.7% |
10 | CNC Machine | 73% | 87% | 19.2% |
C. Author Contributions
- Hardware design: Author A
- Data analysis: Author B
D. Conflict of Interest
No commercial relationships exist with mentioned equipment suppliers.
References
[1] WANG Y, LI Q. IoT-based HMI systems in manufacturing[J]. IEEE Transactions on Instrumentation and Measurement, 2022, 71: 1-12.
[2] 机械工业仪器仪表综合技术经济研究所. OPC UA 工业通信协议性能测试报告[R]. 北京: 机械工业出版社, 2023.
[3] 中国机械工业联合会. 2023 年智能改造白皮书[R]. 北京: 中国机械工业联合会, 2023.